The Solution
As the nationโs third-largest door manufacturer, Steves and Sons produces 3.5 million doors annually. They needed a way to ensure that, from manufacturing to delivery, everything was documented thoroughly.
Steves and Sons leveraged the Laserfiche SDK to ensure top quality manufactured doors and protection from invalid damage claims.
Premium Door Inspection Station
From basic inside door models to premium custom front doors, Steves and Sons manufactures a large range of doors. Since custom doors are very expensive, each one must go through a very thorough inspection process before it is sent out for delivery. This inspection ensures that the door is exactly what the customer ordered and protects the company from future damage claims.
In order to simplify and standardize this inspection process, Tracy developed a custom application called the Premium Door Inspection Station that runs on a special desktop computer in the warehouse. The application walks the door inspector through three different stages in the inspection process:
Stage 1. Verifies that the product is exactly what the customer ordered.
Stage 2. Verifies that the product is free of defects.
Stage 3. Verifies that the product is properly packaged, palletized and labeled.
During Stage 3, the inspector must take some photographs of the product. This is done with a camera that has a wireless internet option to ensure that the photos are automatically transferred back to the desktop computer on which the Premium Door Inspection Station is run.
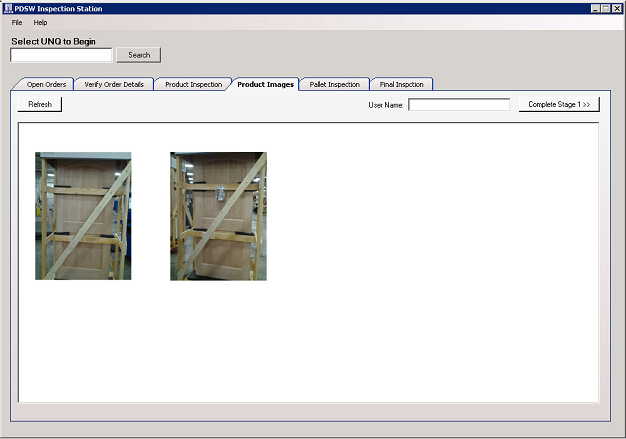
From the application, the inspector sends the photos directly to Laserfiche, where all metadata is automatically applied. Laserfiche is integrated with Siberix Report Writer to generate a custom PDF report of all the details and time stamps of the inspection. This report is also stored in Laserfiche with all metadata automatically applied.
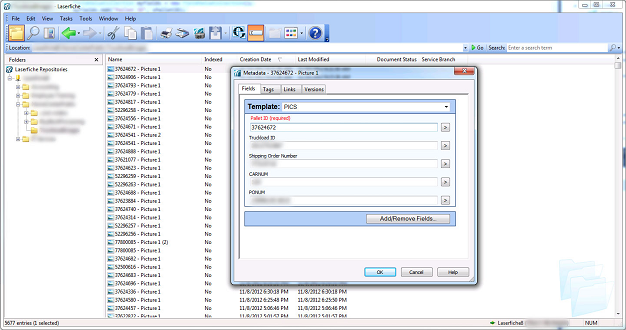
Premium Door Dashboard
Steves and Sons customer service agents deal with calls regarding the status of custom orders, doors being damaged or doors not matching the actual order. To simplify their jobs, Tracy developed a custom Web dashboard that allows the agents to see where exactly in the production cycle a particular door is.
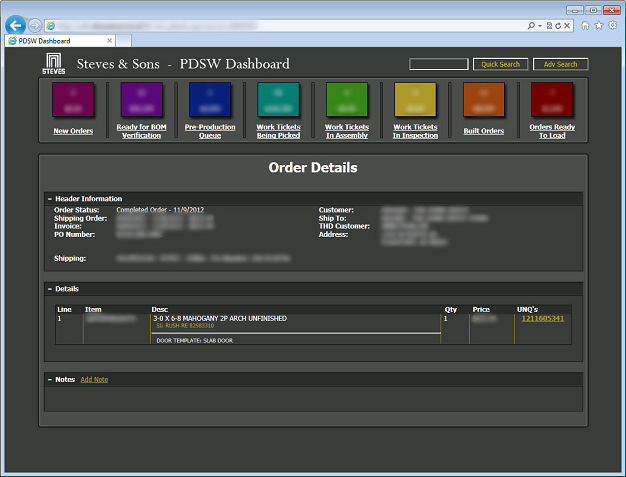
They can clearly see if the particular door is being sanded and stained or at some other part of the production cycle.
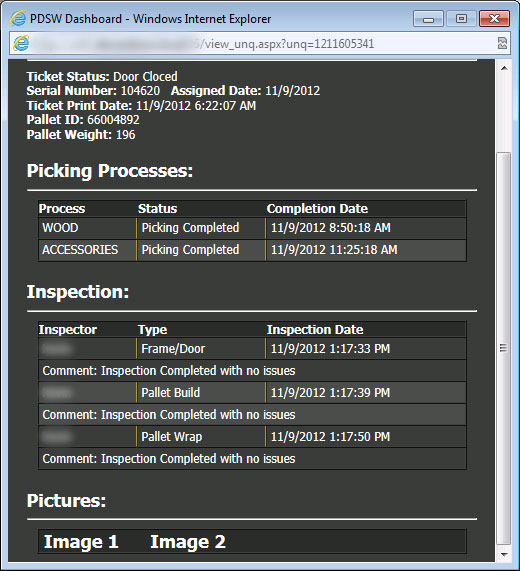
For each order, the customer service agent can also click on a link to view all the photos taken during the inspection. The custom Laserfiche integration searches Laserfiche for the particular Entry ID and then opens up the image in the Web browser.
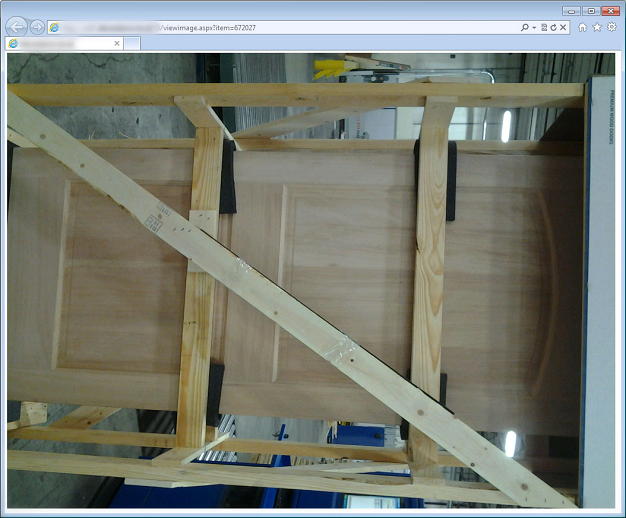
Pallet Image Collection System (PICS)
The majority of our doors (interior doors) are shipped on trucks to stores throughout the Eastern United States. In order to protect Steves and Sons from damage claims when doors are actually damaged during shipping, Tracy developed a Pallet Image Collection System (PICS) custom Android application. This application works as follows:
- As the pallets full of doors are loaded on the delivery truck, the inspector scans each barcode with the Android device. The barcode pulls out information related to the customer and pallet contents from the database and displays it for the inspector.
SASW Mobile View - The inspector verifies this information and is then prompted to take three photos of the pallet with the Android device. These photos are used to file freight damage claims against the truck company if the doors are damaged during shipping.
- The user presses the Submit Pictures button and the photos are automatically sent to a Web Service that opens Laserfiche and stores the images in the repository. The relevant template is automatically applied and the fields populated.
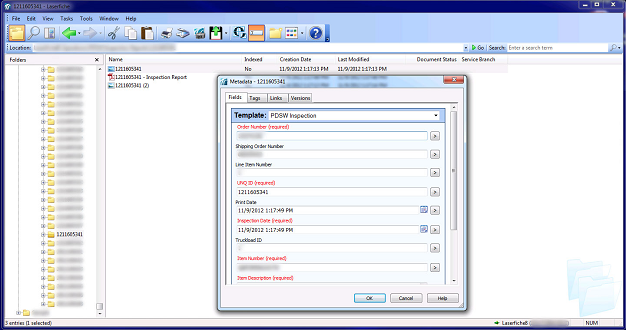
Advantages of the Laserfiche SDK
- The Laserfiche SDK is so easy to use that Tracy was able to create the Package Image Collection System app in a day and a half, without any previous Android programming experience.
- Customer service has greatly improved due to the Premium Door Dashboard.
- The Premium Door Inspection Station and Pallet Image Collection System applications have allowed Steves and Sons to save a lot of money from false damage claims.
- With the Laserfiche SDK, they are saving time by automating tasks. Users donโt have to manually upload photos and apply metadata or even know how to use Laserfiche. Everything is done for them in the background.
Laserfiche Solution Contributors: Laserfiche and Tracy Rickman, Application Developer, Steves and Sons
About Laserfiche Software Development Kit
The Laserfiche SDK is a powerful software development toolkit that allows you to extend your enterprise content management capabilities with the creation of custom solutions. It is the same programming interface that Laserfiche developers use to develop all client-facing applications.
To learn more, contact us today.